The world of industrial machinery and motor testing is evolving rapidly, driven by the need for precision, efficiency, and adaptability. Among the technologies leading this charge are hysteresis-based systems and motor test equipment, which play pivotal roles in industries ranging from automotive manufacturing to renewable energy. This article delves into the intricacies of hysteresis brakes, hysteresis dynamometers, hysteresis clutches, motor dynamometers, and comprehensive motor test systems, highlighting their applications, benefits, and the value they bring to modern engineering challenges.
UNDERSTANDING HYSTERESIS-BASED TECHNOLOGIES
Hysteresis brakes, dynamometers, and clutches operate on the principle of magnetic hysteresis—a phenomenon where the magnetization of a material lags behind the applied magnetic field. This unique property enables precise control over torque and rotational forces without physical contact, reducing wear and tear while enhancing longevity.
HYSTERESIS BRAKES: PRECISION IN MOTION CONTROL
Hysteresis brakes are renowned for their smooth torque delivery and ability to maintain consistent performance across varying speeds. Unlike mechanical brakes that rely on friction, hysteresis brakes use magnetic fields to generate resistance, eliminating the risk of component degradation over time. This makes them ideal for applications requiring fine-tuned control, such as tensioning systems in textile manufacturing or load simulation in aerospace testing.
Key advantages include:
- Zero contact operation, minimizing maintenance.
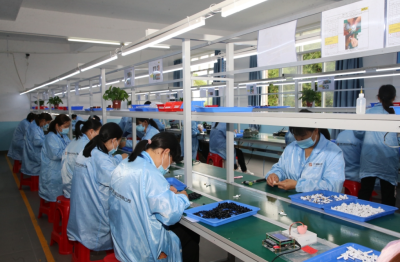

- Linear torque-speed characteristics for predictable behavior.
- Quiet performance, suitable for noise-sensitive environments.
HYSTERESIS DYNAMOMETERS: THE BACKBONE OF POWER MEASUREMENT
In motor testing, hysteresis dynamometers serve as indispensable tools for measuring torque, speed, and power output. By leveraging hysteresis loss, these devices absorb mechanical energy and convert it into heat, allowing engineers to evaluate motor performance under controlled conditions. Applications span from validating electric vehicle drivetrains to optimizing industrial pump efficiency.
Notable features:
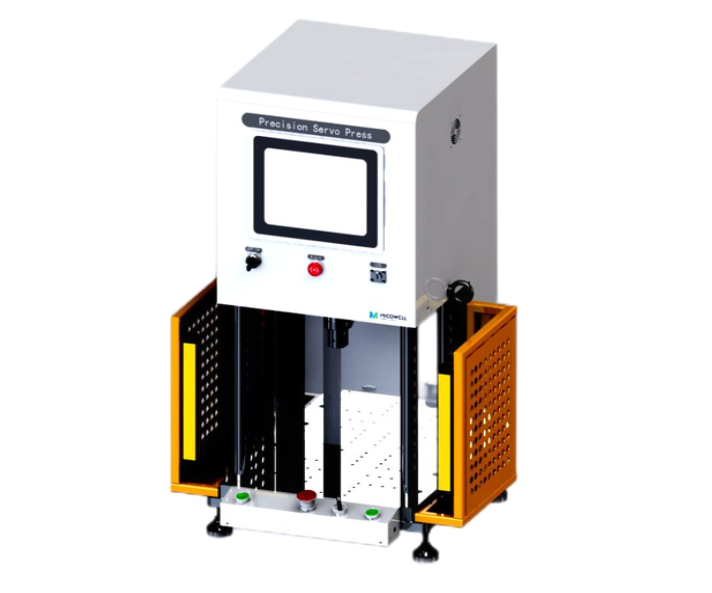
- Wide speed range compatibility.
- High accuracy in transient load simulations.
- Seamless integration with data acquisition systems.
HYSTERESIS CLUTCHES: BRIDGING CONTROL AND RELIABILITY
Hysteresis clutches excel in scenarios demanding slip-free torque transmission and overload protection. Their non-contact design ensures smooth engagement, making them a favorite in packaging machinery, robotics, and precision printing systems. By adjusting the magnetic field strength, operators can fine-tune torque limits dynamically, safeguarding equipment from sudden load spikes.
MOTOR DYNAMOMETERS AND TEST SYSTEMS: ENGINEERING EXCELLENCE UNLEASHED
While hysteresis-based devices focus on controlled energy dissipation, motor dynamometers and test systems provide a holistic approach to motor validation. These systems combine load simulation, data analytics, and real-time monitoring to assess parameters like efficiency, thermal behavior, and durability.
Appliance motor endurance tests : BEYOND BASIC VALIDATION
Today's motor test systems are marvels of integration, incorporating elements such as:
- Regenerative power supplies to reduce energy consumption during testing.
- AI-driven predictive analytics for identifying performance anomalies.
- Modular designs adaptable to diverse motor types, from micro-motors in medical devices to heavy-duty industrial engines.
For instance, in the electric vehicle sector, motor test systems simulate real-world driving conditions—from sudden acceleration to regenerative braking—ensuring motors meet stringent safety and efficiency standards. Similarly, appliance manufacturers rely on these systems to validate the quiet operation and longevity of HVAC motors.
THE SYNERGY OF HYSTERESIS AND MOTOR TESTING TECHNOLOGIES
Combining hysteresis dynamometers with advanced motor test systems creates a powerhouse for R\u0026D and quality assurance. Consider a wind turbine manufacturer testing a new generator design: A hysteresis dynamometer applies variable loads to mimic fluctuating wind conditions, while the motor test system monitors electrical output, vibration, and thermal stability. This integrated approach accelerates development cycles and reduces time-to-market.
CASE STUDY: REVOLUTIONIZING INDUSTRIAL AUTOMATION
A leading robotics company recently integrated hysteresis clutches into its assembly line robots. The clutches' precise torque control enabled delicate handling of electronic components, reducing defect rates by 22%. Concurrently, the firm employed motor dynamometers to test servo motors under extreme duty cycles, achieving a 15% improvement in energy efficiency.
NAVIGATING INDUSTRY CHALLENGES WITH TAILORED SOLUTIONS
Industries face unique testing demands. Aerospace applications, for example, require equipment capable of operating in extreme temperatures and vacuum conditions. Here, hysteresis brakes with specialized cooling systems and motor test rigs equipped with environmental chambers become critical. Conversely, the medical device industry prioritizes compact, sterilizable test systems for micromotors used in surgical tools.
THE ROAD AHEAD: SMART TECHNOLOGIES AND SUSTAINABILITY
Future advancements in hysteresis and motor testing will likely focus on IoT-enabled devices and sustainability. Imagine a hysteresis dynamometer that self-calibrates using embedded sensors or a motor test system that optimizes energy recovery during testing phases. Additionally, as industries push toward net-zero goals, equipment that minimizes energy waste during testing—such as regenerative dynamometers—will gain prominence.
CONCLUSION: EMPOWERING INDUSTRY THROUGH INNOVATION
From hysteresis brakes ensuring precise tension in film production to motor test systems guaranteeing the reliability of next-generation EVs, these technologies form the backbone of modern industrial progress. Their ability to deliver accuracy, durability, and adaptability makes them not just tools, but partners in innovation. As industries continue to evolve, so too will the solutions that test and validate their machinery—ushering in an era where efficiency and reliability are not just goals, but guarantees.
For engineers and decision-makers, investing in cutting-edge hysteresis and motor testing technologies isn’t merely about keeping pace with competitors; it’s about redefining what’s possible. Whether optimizing existing processes or pioneering breakthroughs, these systems provide the foundation for tomorrow’s engineering triumphs.